Project Management and Execution
Establishing the Execution Plan
The execution plan is the core of the contracting program, controlling all expenditure operations on the project and any modifications made during execution. It is created by the technical office or project consultant.
Reference to the execution plan is essential, and strict adherence to the expenditure items in the plan is required. It is not permissible to use any materials that were not previously specified in the plan .
It is responsible for the interconnection between project components through warehouse expenditure permits, return permits, and cash or check expenditure operations, as well as items from site custody and direct purchase operations on sites. This includes the returns of purchases and subcontractor abstracts. Moreover, linking the execution plan to work items enables contracting companies to consistently uncover deviations for each item in the tender compared to the previously estimated values .
Implementing the project according to the execution plan involves dividing the work into:
Self-execution works.
Subcontractor works
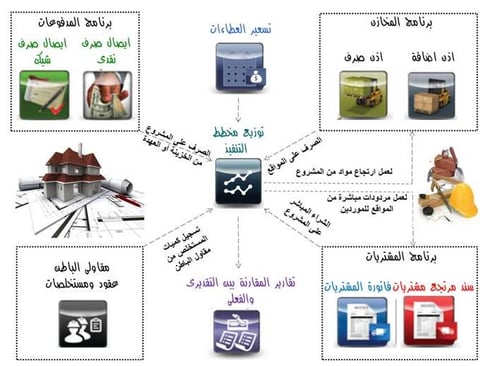
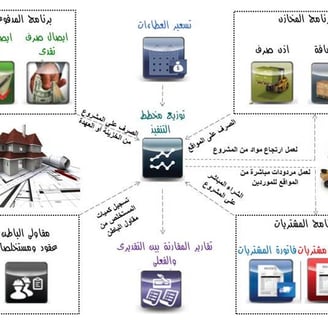
Executing the project according to the execution plan is achieved by dividing the work into:
Self-execution tasks.
Subcontractor tasks.
Self-execution and the executionabstract:
involve the purchase and expenditure of raw materials, as well as the disbursement of expenses, commitments, advances, wages, and insurance on the project. The execution phases are monitored through the execution abstract, serving as a control document within the contracting company (not presented to any external party). It provides a continuous indicator throughout the project for comparing the executed work with the planned values for each project item
Expenditure of Materials and Raw Materials on the Site (A):
During the specified expenditure permit, including quantities, permit number, the site to which the materials are allocated, the person responsible for the expenditure, the warehouse keeper, and the item being expended.
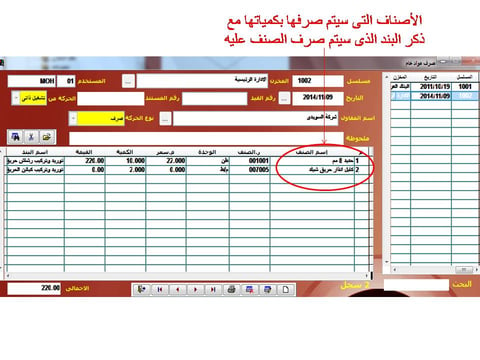
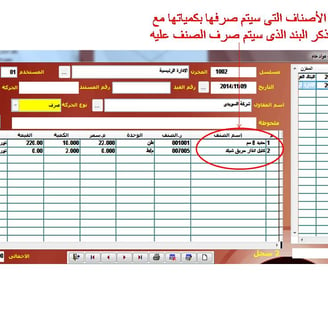
Purchases for the Site (B):
Establish a supplier record detailing the materials supplied by the supplier to the company and their prices.
Create purchase orders specifying the required quantities and the requesting entity (the project).
Issue a purchase order to the supplier, a document recording quantities, prices, delivery schedules, delivery locations, and payment terms.
Receive the purchase invoice, record its data in the program (similar to the supply order but with a different impact on the supplier's account and warehouses).
Issue an accounting entry from the purchase invoice to prove the value of purchases and a cash/cheque payment receipt to the supplier.
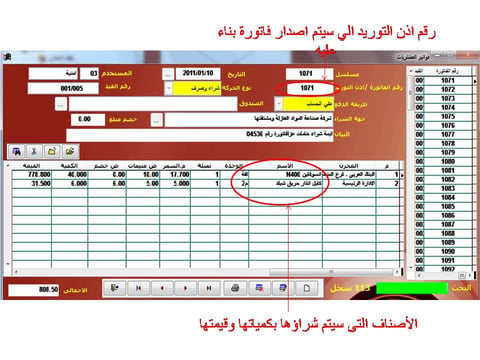
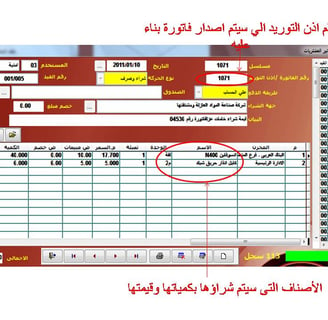
Cash Disbursement from the Treasury (Expenses/Insurance/Commitments/Advances):
This is done through the cyclic process of treasury and bank documents and commitments. Expenditure on the project, such as wages, social insurance, and miscellaneous expenses, occurs through the following documents:
Cash/cheque disbursement receipt from the treasuries and banks.
Cash disbursement from the commitment treasury, specifying the commitment and the person responsible for it.
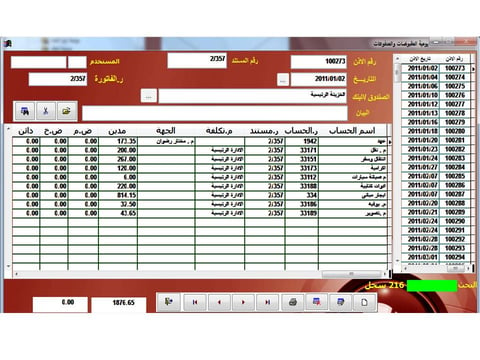
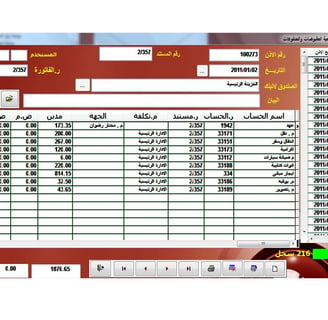