Production System
Defining Products and Production Stages:
The system identifies the components comprising a product (under processing, semi-finished, or finished) with varying proportions or quantities. During production, it assembles these components with specified production deviations, transforming them into a new product with a new average unit price.
Similarly, production occurs in various stages depending on the nature of the product and its processing phases. Production is not limited to direct elements; indirect elements (services) such as water, lighting, and labor can also be added.
The system allows recording the product's component card with the possibility of configurations for a single product. It also enables inputting different production plans, with the system extracting a report on the required quantities of materials for plan execution (purchase plan), considering material balances (actual balance, reserved balance, free balance, goods in transit).
Work Orders and Material Consumption:
The system allows entering and monitoring work order data, extracting a report on the material needs for a specific work order. It provides a report on the net consumed materials for a specific work order and any deviations from standard quantities.
Production Plan Monitoring:
The system tracks the production plan and extracts a report on the production plan status, indicating the planned, executed, and remaining quantities for all items. It also allows generating a cost report for a specific work order or the cost of work orders during a specific period.
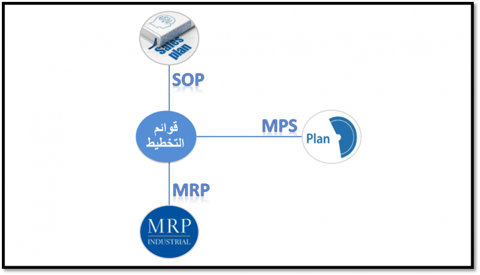
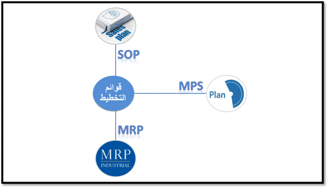